“It is critical to ensure switchboard are operating under optimum conditions, and pro-active maintenance techniques, can help to prevent such losses from switchboard fires happening.”
Every building has a maintenance team to monitor the conditions within. However, we do understand that there are limitations of these teams. They are only able to rectify the situation when it happens.
To identify the conditions of the switchboards and that they are operating under optimum conditions, there are 3 aspects to conduct pro-active maintenance.
- Physical Visual Inspection
- Noise monitoring
- Temperature of switchboards and components
It is easily understood that physical visual inspection and noise monitoring has to be carried out by the maintenance personnel. As for temperature, the current practice is to employ Thermograph expertise whenever a problem is suspected. Some buildings may even conduct annual or once every two years to have thermography conducted. However, this cost is extremely high. This is also not able to pre-empt if a problem is going to occur.
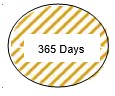
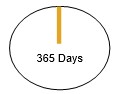
Thermal Strip Indicator provides 24/7, 365 days updates of the temperature of the electrical, and however, thermal scan only provides the specified location, time and date of the scan.
The owners and operators of buildings shall recognize, evaluate and manage their fire and business risks, related to electricity or electrical.
There are numerous numbers of switchboards in every building, and many of them do not have their maintenance done yearly to ensure they are in good working condition. Components of switchboards, are also, many times, not known if they are in their optimum operating conditions.
Electrical fires originated are increasing gradually. It is necessary to reconsider the safety of electricity or electrical and do any prevention possible. The number of electrical fires and business interruptions are probably be reduced specifically by investing in the informing of the risks caused by electricity or electrical, and by encouraging them to use the equipment safely and maintain it in an organized manner.
Some felt that short duration of power failures or power disruptions are fine. However, many have underestimated the consequences, especially those not so obvious or are indirectly affecting the production, services and facilities. They are mainly caused by or began with a power failure. A significant voltage drop, which can cause machinery to trip, has the same consequences as total power loss. There are incidents when an actual power interruption occurred, caused production/operation activities to a halt. This had not only caused business interruptions, but also damages to facilities and system.
Ease of Detection of faulty electrical components
Assist in detecting overheating problems, minimising breakdowns occurrence.
Real time indicator of temperature, Non-Intrusive, No Shutdown Time required for installation.
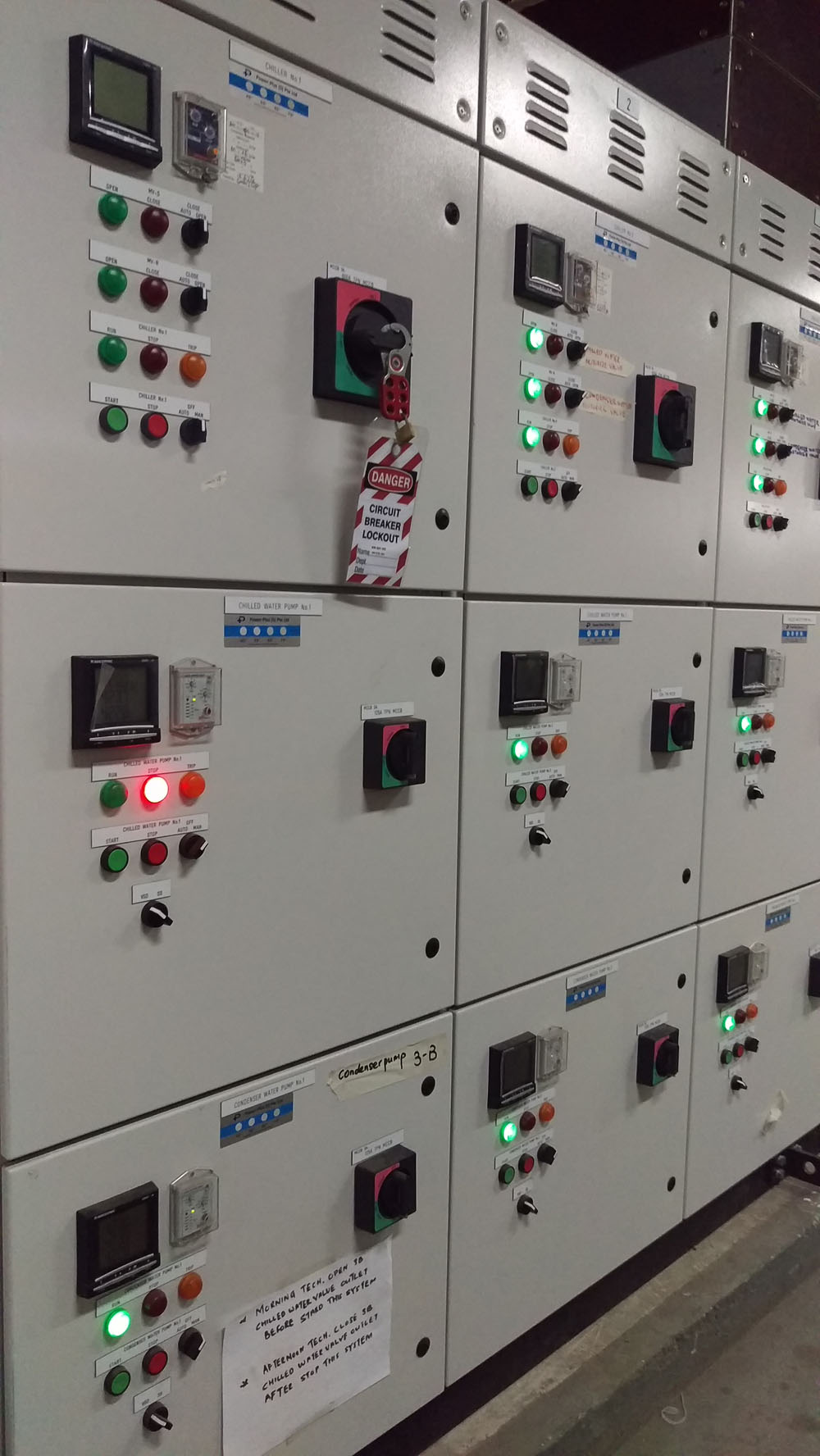
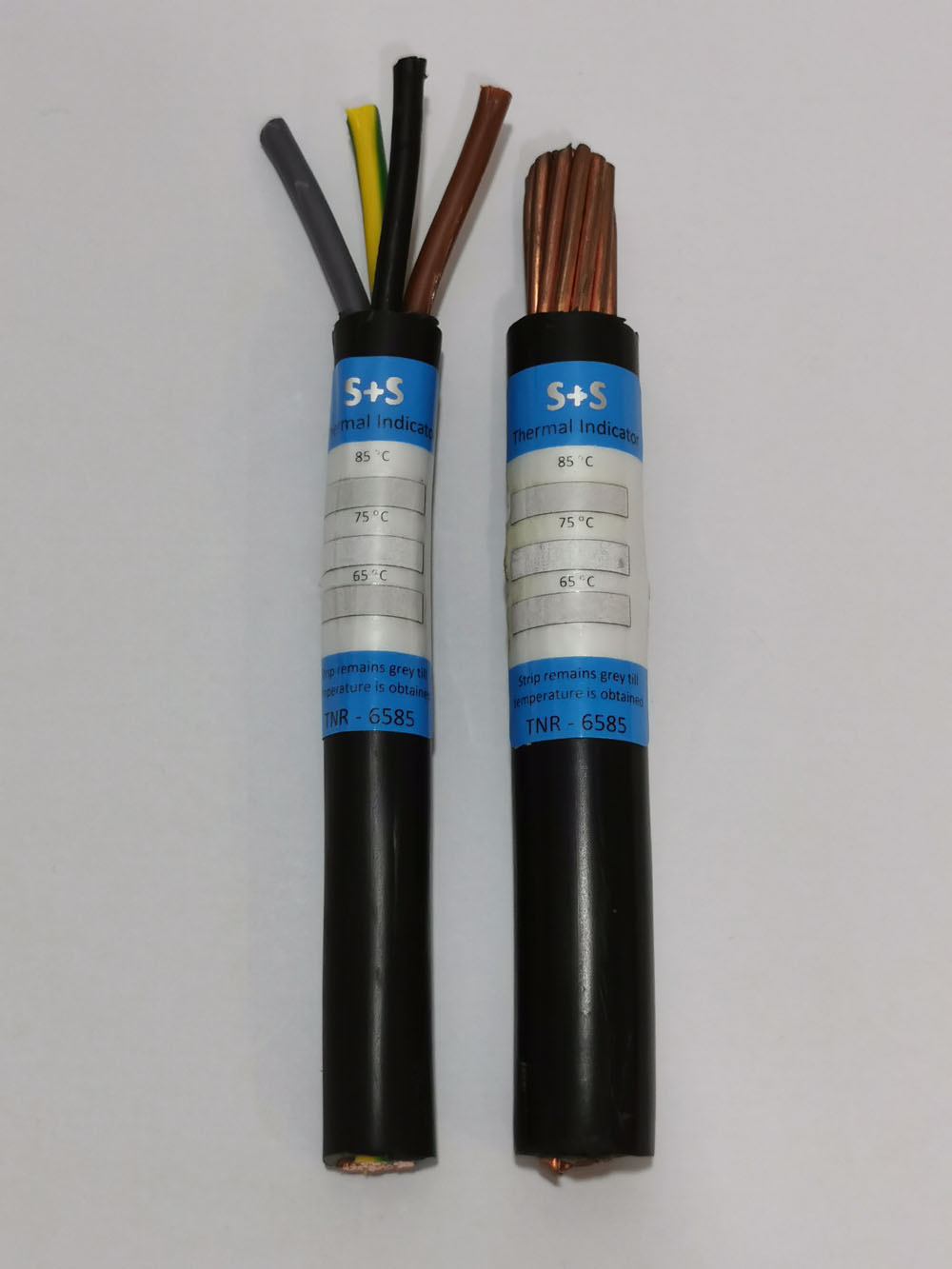
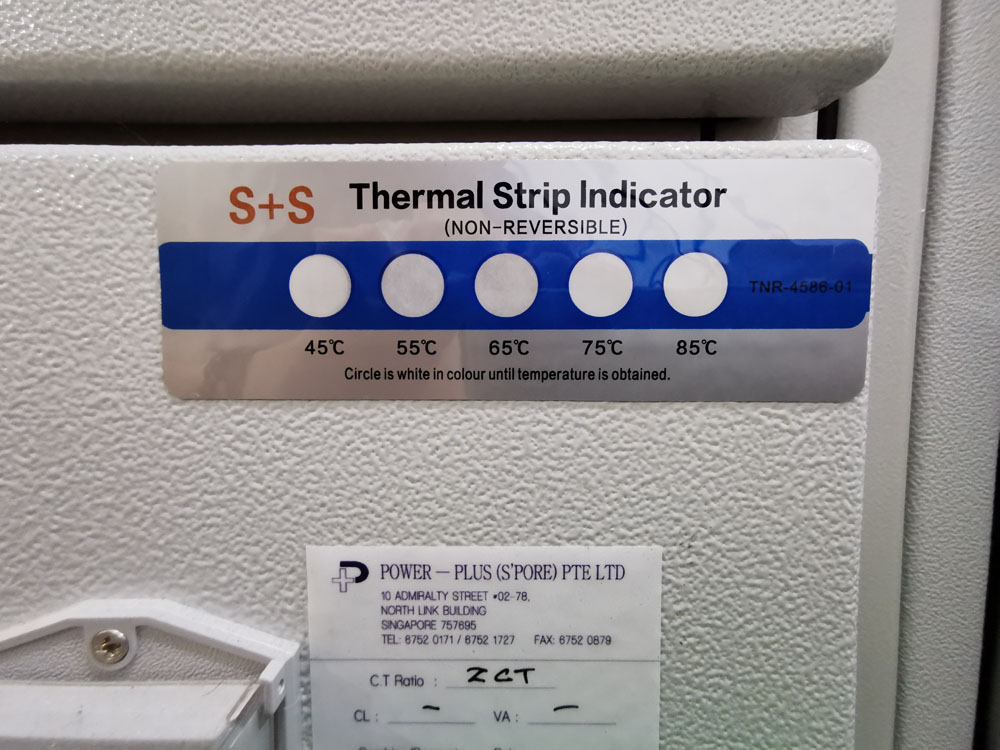
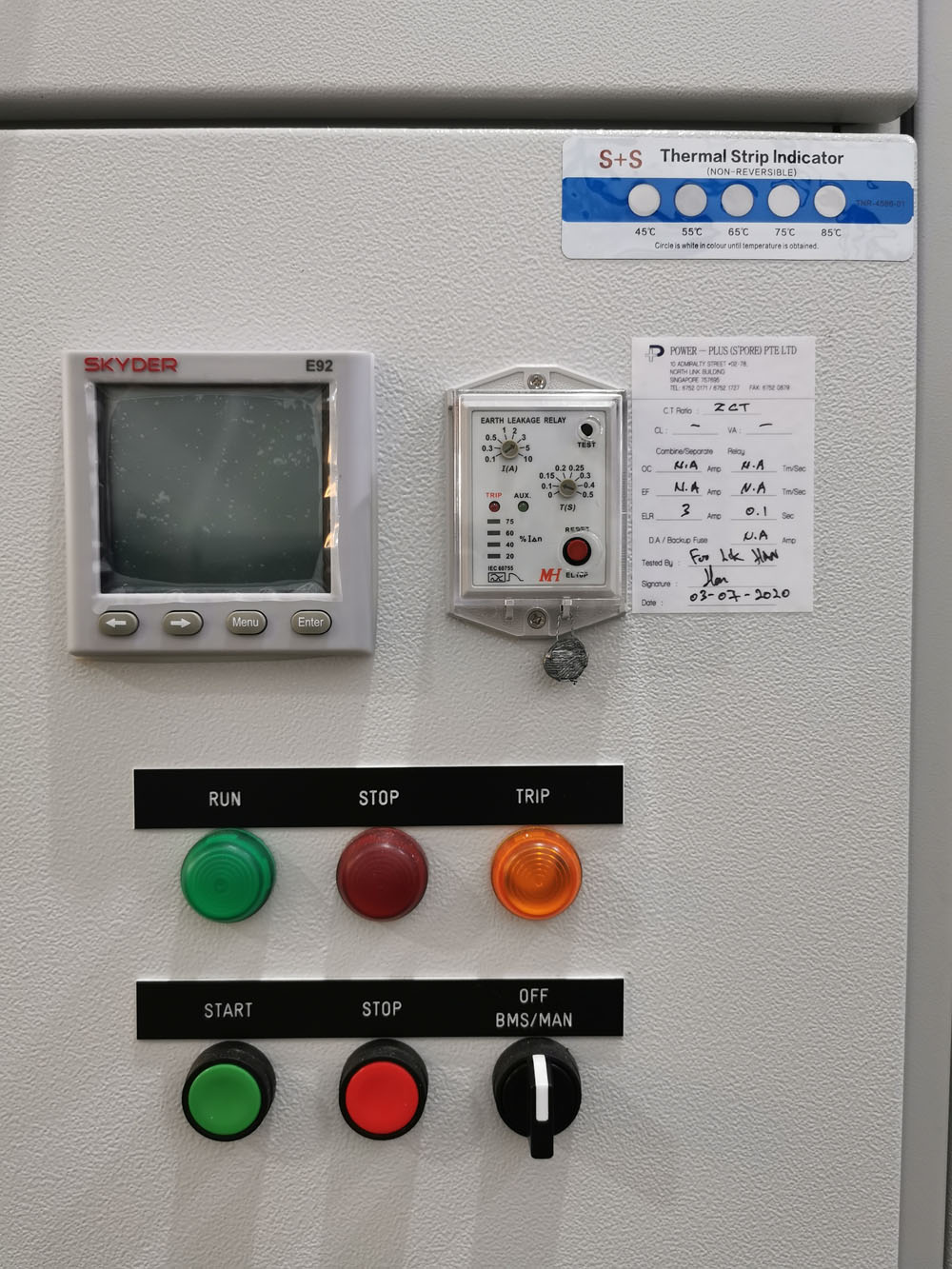